In 2016, one of the largest battery wholesalers in North America, which already had considerable manufacturing experience with lead-acid batteries, decided to launch their first lithium-based product: an LFP battery pack for industrial equipment (mainly floor scrubbers).
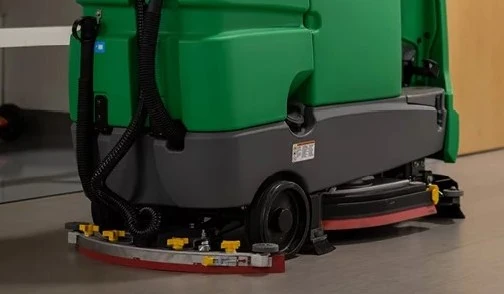
The main application were small industrial vehicles.
Challenge
Designing a new battery product from scratch can be an intimidating task, especially for a team that is new to lithium batteries. Other than deciding on the right chemistry and cell type, safety certification was also a concern since the customer was not familiar with the technical requirements and testing procedures.
Approach
The customer reached out to the founder of DSC Energy as an external consultant to help them define the battery pack’s chemistry and specifications, find a cell supplier and recruit the team that would be in charge of the BMS and mechanical design, as well as managing the entire testing and certification process.
Solution
Through DSC, the customer was able to recruit an experienced senior engineer to strengthen their own design capabilities. After confirming the supplier of the battery cells, the technical team started working on the BMS and pack design, under our supervision.
We helped design the battery pack and BMS, establish a supply chain and draft the BOM
A local supply chain was established, and DSC helped draft the BOM and find a suitable ODM partner in Taiwan, where an assembly line was set up and operators were trained according to a previously defined SOP. The line’s pilot run was successfully completed within six months.